Hybrid and Electric Vehicles Training
The Hybrid and Electric Vehicle Training Program is an in-depth, hands-on course designed to provide participants with the knowledge and skills required to understand, design, and maintain hybrid and electric vehicles. The program covers essential topics such as battery technology, electric drivetrains, power electronics, charging systems, and energy management. Participants will also gain proficiency in programming and diagnostics tools used in hybrid and electric vehicle systems.
Ideal for automotive engineers, technicians, and technology enthusiasts, this program offers flexible learning options, expert guidance, and an industry-recognized certification. By the end of the course, participants will be equipped to work on hybrid and electric vehicle systems, contributing to the growth of sustainable transportation in industries ranging from automotive to energy and beyond.
4.8
In collaboration with
Why Choose Skillairo?
Expert-Led Training
Internship experience
Industry Relevent Curriculum
Hands-On Projects
LMS Access
Comprehensive Tools and Technologies
professional certifications
Career Support
TRAINING PATH
SKILLS COVERED
INDUSTRY PROJECTS
Electric Vehicle Powertrain Simulation
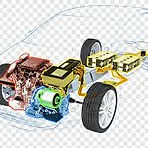
Create a simulation of the electric vehicle (EV) powertrain, including components like the motor, inverter, and battery. Model energy flow, efficiency, and performance to optimize the vehicle's power usage and overall system design. The key component include 1.System Architecture and Design Define the key components of the electric vehicle powertrain, including the electric motor, battery pack, power electronics, and transmission system, ensuring compatibility and optimal performance across the entire system. 2.Battery Performance Simulation Simulate the behavior of the battery pack under various driving conditions to assess energy consumption, charging/discharging rates, and overall efficiency. This includes evaluating battery life, degradation, and thermal management strategies. 3.Motor and Inverter Simulation Model the electric motor’s performance, including torque, power output, efficiency, and dynamic behavior, alongside the inverter that controls power flow between the battery and motor. 4.Drive Cycle Simulation Simulate various driving cycles (e.g., city, highway, stop-and-go) to evaluate how the powertrain performs in different real-world scenarios, assessing energy usage, acceleration, and regenerative braking effectiveness. 5.Energy Efficiency and Regenerative Braking Evaluate the powertrain’s overall energy efficiency, considering energy recovery during braking and the effectiveness of regenerative braking systems in extending battery life and increasing range. 6.Thermal Management Simulation Model the thermal behavior of key powertrain components (motor, inverter, battery) to ensure they operate within optimal temperature ranges and avoid overheating. This includes analyzing cooling systems and thermal management strategies. 7.Vehicle Range and Efficiency Estimation Estimate the EV's driving range under different conditions and driving cycles, optimizing the balance between power delivery, battery size, and overall vehicle weight. 8.Driveability and Performance Optimization Simulate the vehicle’s acceleration, top speed, and handling characteristics to fine-tune the performance for the desired customer experience while optimizing for efficiency and power delivery. 9.System Integration and Control Strategies Model the interaction between the powertrain components and control systems, such as the energy management system (EMS), which optimizes the operation of the motor, battery, and inverter to maximize performance and range. 10.Compliance with Standards Ensure the powertrain design meets industry standards for performance, safety, and regulatory requirements, including those for emissions (where applicable), safety, and efficiency. 11.Documentation and Reporting Generate detailed simulation reports, including performance metrics, efficiency data, and recommendations for optimization, providing insights for further development and refinement of the powertrain system. Technologies MATLAB/Simulink (system modeling and simulation), Simpack or Adams (vehicle dynamics simulation), ANSYS (thermal and structural analysis), AVL Cruise (powertrain simulation), GT-SUITE (multidomain simulation), and MATLAB/Simulink (battery and motor modeling). Outcome A comprehensive electric vehicle powertrain simulation that analyzes and optimizes key performance metrics, such as energy efficiency, range, power output, and thermal management. The simulation will support the development of an EV powertrain design that balances performance, cost, and sustainability while meeting regulatory requirements.
Hybrid Vehicle Energy Management System

Develop an energy management system for hybrid vehicles that optimally switches between the internal combustion engine and electric motor based on driving conditions. Use algorithms to balance fuel consumption, emissions, and battery life. The key component include 1.System Architecture and Design Define the hybrid vehicle's powertrain components, including the internal combustion engine (ICE), electric motor, battery, and energy management system (EMS), ensuring smooth integration and coordination between these components. 2.Energy Distribution Strategy Develop algorithms that govern the power split between the ICE and electric motor based on factors like speed, load, battery charge, and driving conditions. The goal is to minimize fuel consumption while maintaining optimal performance. 3.Battery Management and Regeneration Model and optimize battery charging and discharging cycles to ensure efficient energy use. Simulate regenerative braking systems to recover energy during braking and store it back in the battery, enhancing overall vehicle range and efficiency. 4.Driving Mode Selection Design driving modes (e.g., electric-only, hybrid, power mode) that dynamically adjust the operation of the vehicle’s powertrain, selecting the best combination of ICE and electric motor power based on driving conditions and the battery state of charge. 5.Energy Flow Control Simulate energy flow between the electric motor, ICE, battery, and power electronics. Develop control strategies that optimize fuel efficiency by reducing reliance on the ICE in low-load conditions and leveraging the electric motor for short-distance driving or stop-and-go traffic. 6.Thermal Management for Powertrain Simulate the thermal behavior of the engine, motor, and battery pack. Design a thermal management system to ensure that components operate within safe temperature limits, improving system reliability and efficiency. 7.Fuel Economy and Emissions Optimization Simulate and optimize fuel consumption and emissions performance by fine-tuning the EMS to reduce fuel usage in different driving scenarios, such as city, highway, and combined driving cycles. 8.Vehicle Performance Optimization Analyze vehicle acceleration, driving dynamics, and handling to ensure a balanced performance between power from the electric motor and the ICE. Optimize for both driving performance and energy efficiency. 9.Charging and Battery Health Management Design strategies for managing battery charging cycles, including charging rates, state-of-charge (SOC) limits, and battery health monitoring. This ensures long battery life while minimizing the dependency on the ICE when possible. 10.System Integration and Communication Model the communication and coordination between the EMS, vehicle control unit (VCU), powertrain components, and sensors. Ensure smooth system operation with real-time feedback for optimal performance. 11.Documentation and Reporting Generate simulation reports that provide performance metrics such as fuel economy, battery state-of-charge, energy flow data, and efficiency calculations. These reports will support further optimization and refinement of the EMS. Technologies MATLAB/Simulink (system modeling and control algorithm development), Simpack or Adams (vehicle dynamics simulation), AVL Cruise (powertrain simulation), dSPACE (real-time simulation and hardware-in-the-loop testing), GT-SUITE (multidomain simulation), and Modelica (multi-physics system simulation). Outcome A fully optimized Hybrid Vehicle Energy Management System that enhances fuel efficiency, reduces emissions, and maximizes vehicle performance by intelligently managing the power split between the ICE and electric motor. The system will ensure a smooth and efficient driving experience while maintaining battery health and maximizing energy recovery.
EV Charging Station Network Design
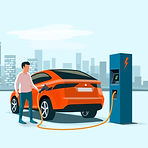
Design a network of EV charging stations, including location planning, power supply integration, and user accessibility. Consider factors like traffic patterns, station capacity, and ease of use to optimize the network for electric vehicle owners. The key component include 1.Site Selection and Feasibility Study Conduct a thorough analysis of potential locations for the EV charging stations, considering factors like proximity to major roadways, urban centers, residential and commercial areas, grid connectivity, and user accessibility. Analyze demand forecasts and identify key areas with high EV usage. 2.Charging Infrastructure Design Design the infrastructure for each station, including the number and types of chargers (Level 1, Level 2, DC fast chargers), electrical connections, power distribution systems, and safety features. Ensure scalability and adaptability to future technological advancements. 3.Power Supply and Grid Integration Evaluate the power supply requirements for each station, ensuring the local grid can support the demand. Design power management systems to efficiently distribute electricity to multiple chargers, considering peak usage times and load balancing. 4.Charging Station Layout and User Experience Develop a user-friendly layout for each charging station, optimizing for easy access, clear signage, parking spaces, and safety. Consider additional services such as rest areas, Wi-Fi, and payment systems to improve the overall user experience. 5.Smart Charging and Load Management Implement smart charging systems that dynamically adjust charging speeds based on grid demand, time-of-day pricing, and vehicle state of charge. Develop algorithms to manage the distribution of power efficiently across multiple charging points to avoid overloading the grid. 6.Network Connectivity and Monitoring Design a centralized monitoring system that allows real-time tracking of charging station status, usage data, and performance. Ensure the system supports remote diagnostics, payment processing, and user feedback, providing a seamless charging experience. 7.Energy Source and Sustainability Incorporate renewable energy sources, such as solar panels, into the charging station design to reduce the carbon footprint and operational costs. Evaluate energy storage solutions to store surplus energy and improve grid resilience during peak demand. 8.Security and Safety Ensure the charging stations are equipped with necessary safety measures, such as emergency shut-off systems, fire prevention, and secure payment methods. Design systems to protect both the infrastructure and users from potential hazards. 9.Data Management and Reporting Develop a data management system to track energy usage, charging times, and customer interactions. Generate reports to optimize station performance, plan for future expansion, and analyze system efficiency and usage patterns. 10.Regulatory Compliance Ensure that the charging station network complies with local, national, and international regulations regarding safety, accessibility (ADA compliance), and grid connection standards. 11.Expansion and Scalability Planning Design the network with future expansion in mind, ensuring that stations can be added or upgraded as demand for EV charging increases and as technology advances. Technologies AutoCAD or Revit (site planning and infrastructure design), MATLAB/Simulink (smart charging algorithms), SCADA systems (real-time monitoring), GIS tools (site selection and analysis), PowerFlow (grid integration and power distribution), and EVSE software for network management and reporting. Outcome A comprehensive and scalable EV charging station network design that optimizes site locations, charging infrastructure, user experience, and sustainability. The network will support the growing demand for electric vehicles by providing accessible, efficient, and user-friendly charging solutions while promoting renewable energy use and grid stability.
Battery Management System for Electric Cars

Build a battery management system (BMS) for electric vehicles that monitors and regulates the charging, discharging, and health of the battery pack. Implement algorithms for battery state estimation, fault detection, and performance optimization. The key component include 1.Battery Pack Design and Integration Define the specifications and architecture of the battery pack, including the type of cells, configuration (series/parallel), and integration with the vehicle’s powertrain. The BMS will manage the interactions between the battery pack and other powertrain components (motor, inverter). 2.State of Charge (SOC) Estimation Develop algorithms to accurately estimate the battery's state of charge (SOC), which represents the remaining energy in the battery. This involves real-time monitoring of voltage, current, and temperature to predict SOC with high precision. 3.State of Health (SOH) Monitoring Implement algorithms to assess the battery's state of health (SOH), which indicates the overall condition of the battery and its ability to hold charge. SOH will be calculated based on factors such as battery capacity degradation, charge/discharge cycles, and temperature variations. 4.Charge/Discharge Control Design the BMS to manage safe and efficient charge and discharge cycles. This includes controlling the charging rate, preventing overcharging or deep discharging, and ensuring that charging is performed within the optimal voltage and current ranges to maintain battery life. 5.Thermal Management Incorporate a thermal management system to monitor and control the temperature of the battery pack. The BMS will control cooling and heating systems to ensure that the battery operates within the ideal temperature range, preventing overheating or freezing, which could degrade performance and lifespan. 6.Cell Balancing Implement passive or active cell balancing mechanisms to ensure all cells in the battery pack remain at an equal charge level, optimizing the pack’s performance and preventing over-discharge or overcharge in individual cells. 7.Battery Protection and Safety Integrate safety mechanisms to protect the battery from overvoltage, undervoltage, overcurrent, short circuits, and thermal events. The BMS will be responsible for triggering alarms or disconnecting the battery pack if hazardous conditions are detected. 8.Energy Efficiency and Power Management Monitor and manage the energy flow from the battery to the vehicle’s powertrain, ensuring that power is delivered efficiently. The BMS will work in coordination with the vehicle’s energy management system (EMS) to optimize energy consumption and maximize driving range. 9.Data Logging and Communication Enable data logging and communication with the vehicle’s onboard diagnostics (OBD) system. This will allow continuous monitoring and real-time feedback on battery health, performance, and usage, facilitating maintenance and troubleshooting. 10.Battery Diagnostics and Fault Detection Integrate diagnostic tools to detect potential faults in the battery pack, such as faulty cells, connections, or wiring. The BMS will provide alerts for preventative maintenance and notify drivers about battery-related issues in real-time. 11.Lifecycle Management and Battery Replacement Alerts Track the lifecycle of the battery, providing alerts when the battery reaches the end of its optimal performance or requires maintenance. The BMS will help plan for battery replacement or refurbishment. Technologies MATLAB/Simulink (system modeling and control algorithms), CAN protocol (communication with vehicle systems), NI LabVIEW (data acquisition and monitoring), LTSpice or PSIM (battery simulation), and embedded systems (microcontroller-based BMS design). Outcome A fully integrated and optimized Battery Management System for electric vehicles that ensures efficient energy use, enhances battery longevity, improves safety, and maximizes vehicle range. The system will provide real-time monitoring, data logging, and diagnostics to maintain optimal battery performance and facilitate proactive maintenance.
Vehicle-to-Grid (V2G) System Development
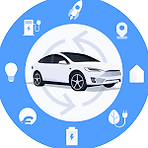%20System%20Development.png)
Develop a Vehicle-to-Grid (V2G) system that allows electric vehicles to return energy to the grid when not in use. Use smart grid technology to manage energy flow, optimize charging and discharging schedules, and reduce energy costs for users and utilities. The key component include 1.System Architecture and Design Design the architecture of the V2G system, integrating EVs with the grid infrastructure. This includes the development of bidirectional chargers, communication protocols, and coordination mechanisms between the EVs, charging stations, and the grid operator. 2.Bidirectional Charging and Power Flow Control Develop algorithms for managing bidirectional power flow, enabling EVs to charge from the grid and discharge back to the grid. The system will ensure that the energy flow is controlled based on grid demand, vehicle battery state of charge (SOC), and other factors such as pricing and user preferences. 3.Communication Protocols and Standards Implement standardized communication protocols (e.g., ISO 15118, OCPP) for real-time data exchange between the EV, charging stations, and the grid. This includes information on energy consumption, SOC, charge/discharge requests, and grid conditions, ensuring seamless coordination and control. 4.Grid Integration and Energy Management Design and simulate grid integration models that allow EVs to support grid balancing, frequency regulation, and peak load shaving. The V2G system will work with the grid operator’s energy management system (EMS) to respond to grid signals and optimize energy distribution based on grid demand and supply. 5.Battery State of Charge (SOC) Management Develop algorithms to ensure that the battery SOC is carefully managed during V2G operations. The system will prevent over-discharge or deep discharge of the battery, while ensuring that the vehicle is charged to an optimal level when the driver needs it. 6.Demand Response and Peak Shaving Implement demand response strategies that leverage the energy stored in EV batteries to reduce grid stress during peak demand periods. The V2G system will contribute to peak shaving by discharging power from EVs to the grid during high-demand times, reducing the need for expensive and carbon-intensive backup power. 7.Energy Pricing and Market Participation Integrate dynamic pricing mechanisms that allow EV owners to participate in energy markets, optimizing charging and discharging times to take advantage of lower energy prices or incentivize grid services. The system will allow EVs to discharge power to the grid when it’s most economically beneficial for the owner and the grid. 8.Safety and Grid Protection Ensure that the V2G system includes safety protocols to protect both the EVs and the grid from power surges, faults, or other potential issues. The system will incorporate protections such as overcurrent protection, voltage regulation, and automatic disconnecting of the EV from the grid if necessary. 9.User Interface and Control Design user-friendly interfaces for EV owners to monitor and control V2G operations, such as setting charging/discharging preferences, scheduling, and managing participation in demand response programs. This interface will provide real-time feedback on energy flow, costs, and energy savings. 10.Data Monitoring, Logging, and Reporting Develop systems for continuous monitoring, data logging, and reporting of V2G activities. The system will track parameters such as energy transferred to/from the grid, charging times, and battery health, generating reports for performance analysis, maintenance, and optimization. 11.Regulatory Compliance and Standards Ensure that the V2G system complies with local, national, and international regulations, including grid standards, safety protocols, and certification requirements for EV chargers, communication, and bidirectional energy flow. Technologies MATLAB/Simulink (system modeling and control algorithms), V2G communication protocols (ISO 15118, OCPP), Smart Grid Simulation Software (e.g., DIgSILENT PowerFactory, GridLAB-D), IoT (for real-time data collection and monitoring), CAN protocol (for vehicle communication), and embedded systems (for bidirectional charger design and control). Outcome A fully functional Vehicle-to-Grid (V2G) system that allows electric vehicles to contribute to grid stability, optimize energy use, and enable efficient energy exchange. The system will enhance the integration of renewable energy sources, reduce energy costs, and provide a valuable service to both EV owners and the grid operator, while ensuring safety, regulatory compliance, and user convenience.
CERTIFICATIONS
Get certified in Hybrid and Electric Vehicles through our program and receive both a Training Completion Certificate and an Internship Completion Certificate. The prestigious Top Performer Certificate is awarded to outstanding students who performed exceptionally well during both the training and internship phases.
PRICING PLAN
HYBRID AND ELECTRIC VEHICLES INDUSTRY TRENDS
These trends underscore India's expanding role in the global Hybrid and Electric Vehicles landscape, supported by a robust IT industry and a growing pool of skilled professionals.
45.16% Annual Growth Rate
The hybrid and electric vehicle (EV) market in India is undergoing rapid expansion, driven by environmental awareness and government initiatives. In the fiscal year 2023, approximately 2.64 million hybrid vehicles were sold, with projections estimating sales to reach about 14.06 million by FY 2028, reflecting a compound annual growth rate (CAGR) of 45.16% during the FY 2024–FY 2028 period.
This growth is supported by government programs like the Faster Adoption and Manufacturing of Hybrid and Electric Vehicles (FAME) scheme, which provides incentives to both manufacturers and consumers.

Other key industry trends
-
In the first quarter of 2024, strong hybrid passenger vehicles held a 2.5% share of India's passenger vehicle market, marking an increase from the previous quarter.
-
While specific revenue percentages are not readily available, India's EV market is expanding, with projections indicating that pure EVs may constitute less than 7% of new car sales by 2033, suggesting a gradual yet steady growth trajectory.
-
The Indian government's EV30@30 initiative aims for EVs to account for 30% of new car sales by 2030. However, current trends suggest that achieving this target may require enhanced policy measures and infrastructure support.
Source: Grand View Research, IMARC
INR 5-20L Annual Salary
In India, professionals specializing in hybrid and electric vehicle (EV) engineering earn varying salaries based on experience and location. Entry-level positions typically offer annual salaries starting at approximately ₹500,000, while experienced engineers can earn up to ₹2,000,000 per year. Salaries are influenced by factors such as specific expertise, employer, and regional demand
.
The hybrid and EV industry in India is experiencing significant growth. Hybrid car sales surged by 27% in the first seven months of 2024, totaling 51,897 units, driven by strong hybrid models. In contrast, battery electric vehicle (BEV) sales increased by 10% during the same period, reaching 54,118 units. This trend indicates a growing acceptance of hybrid vehicles among Indian consumers.

OUR ALUMNI Work At
Our alumni are already pushing boundaries in their fields. Former students are excelling in high-profile industries and influencing the landscape of tomorrow.








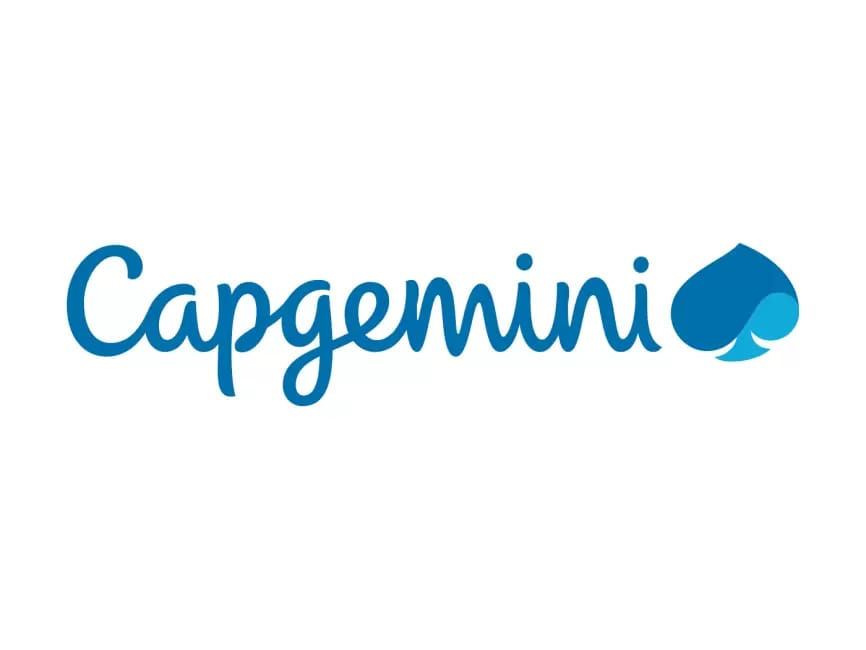
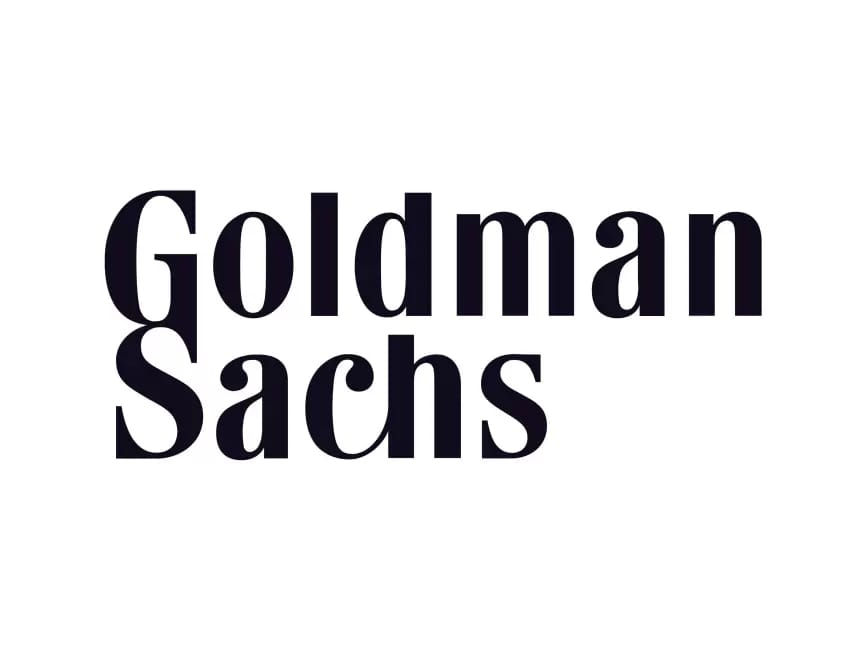




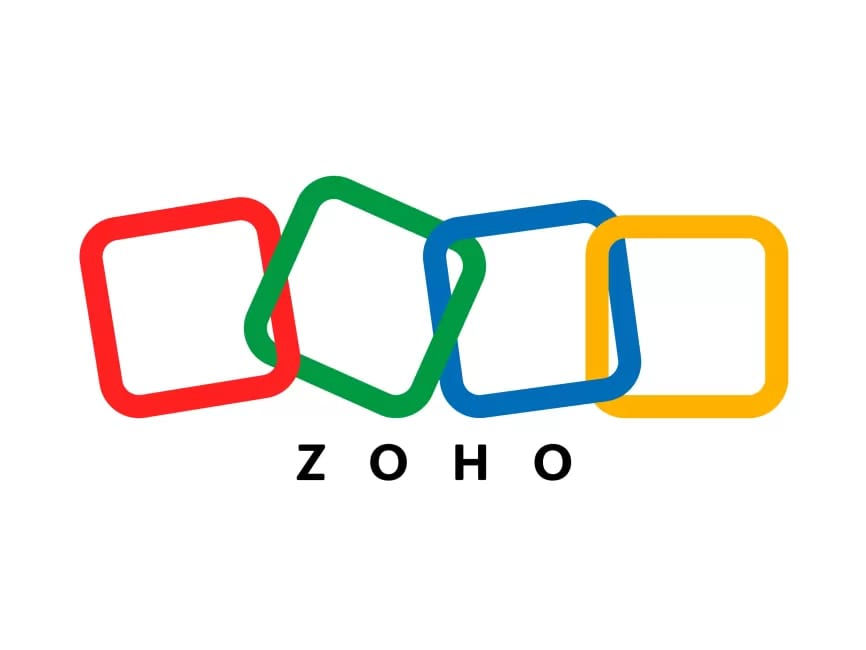

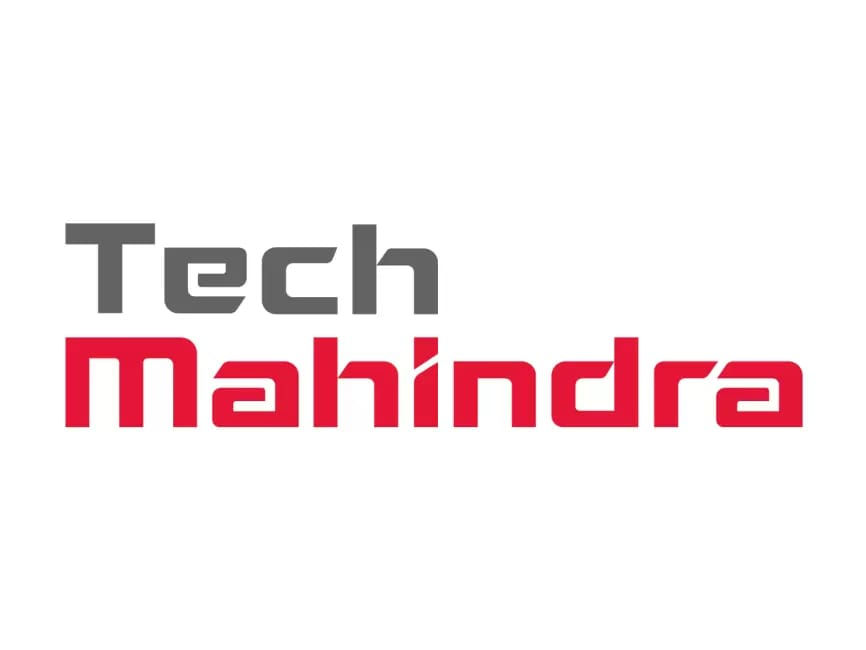

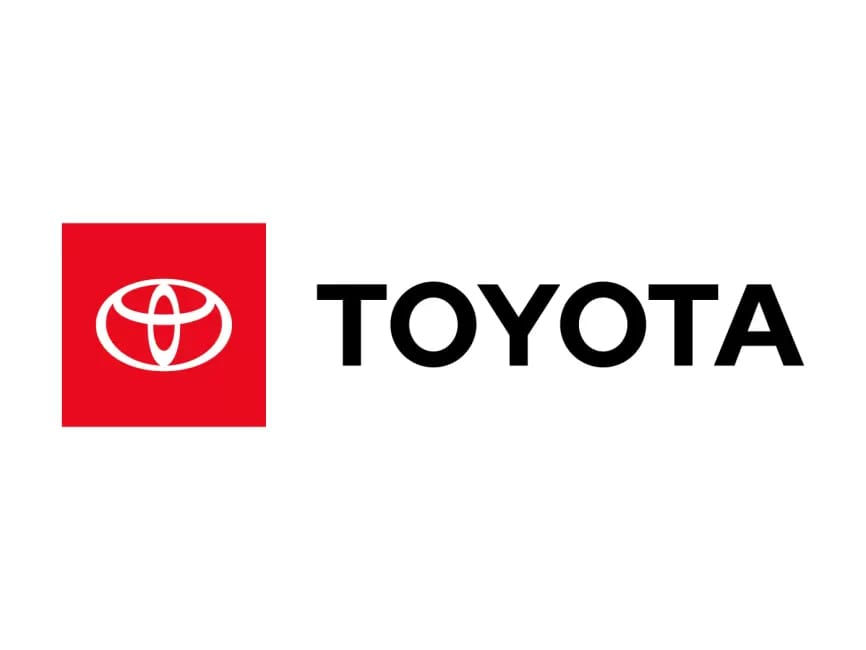



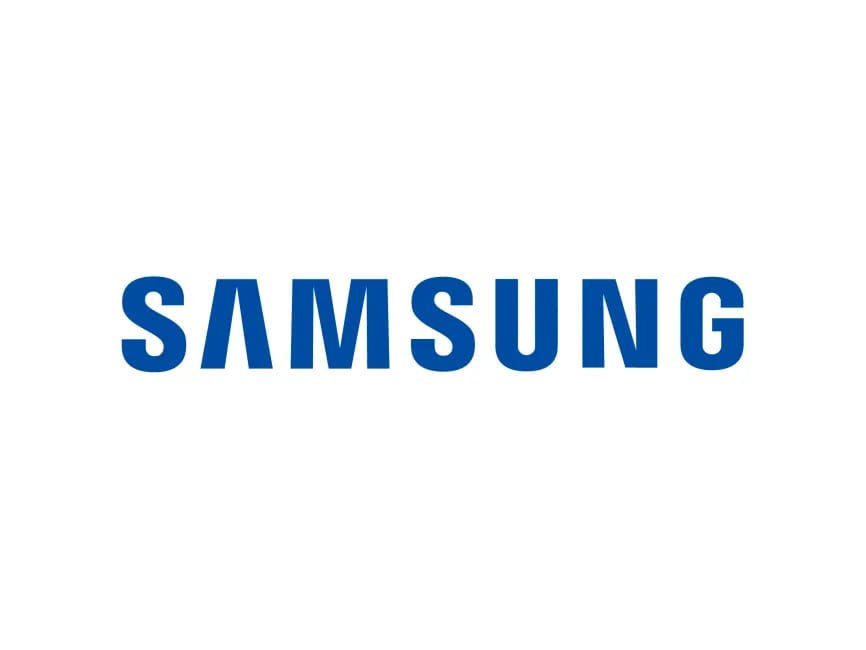
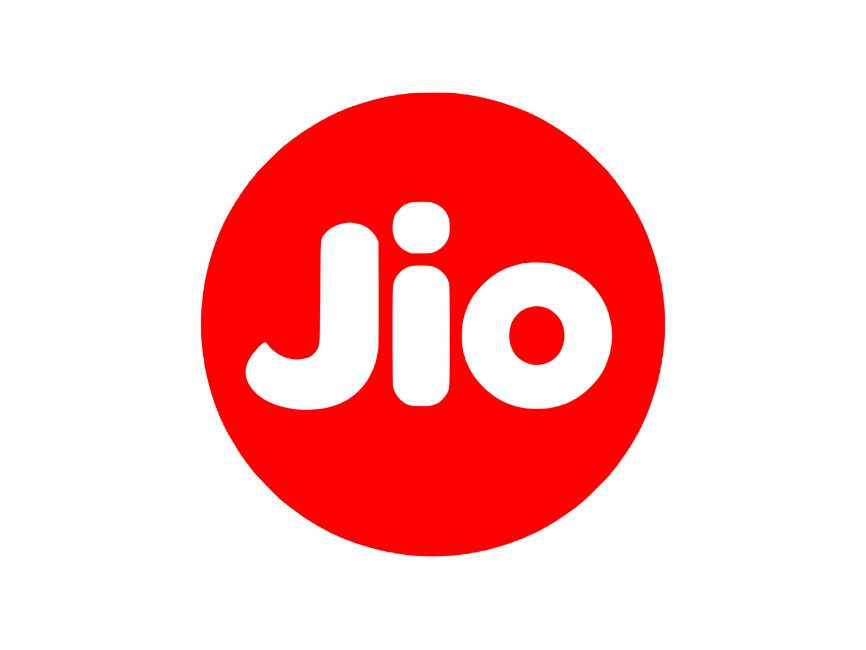




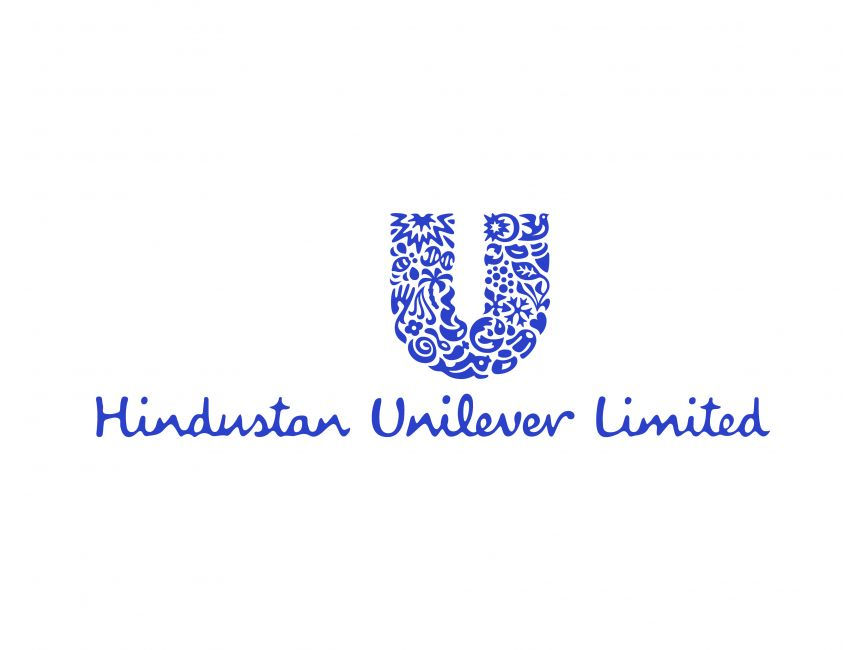





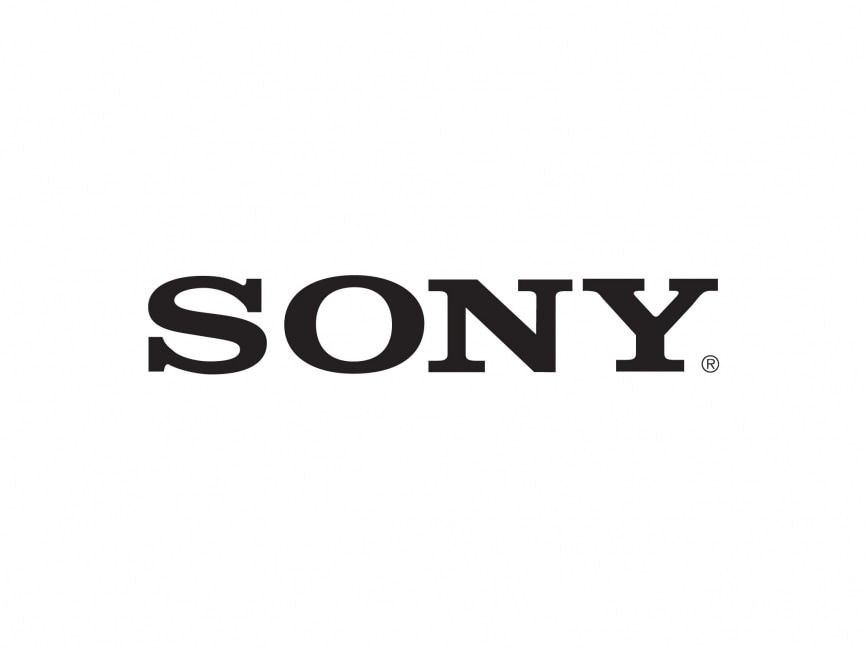



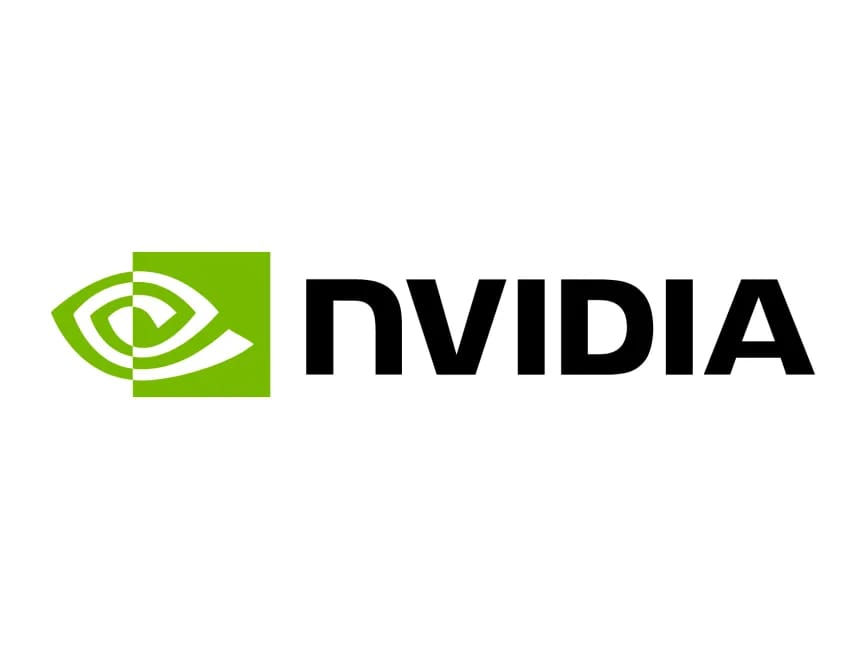

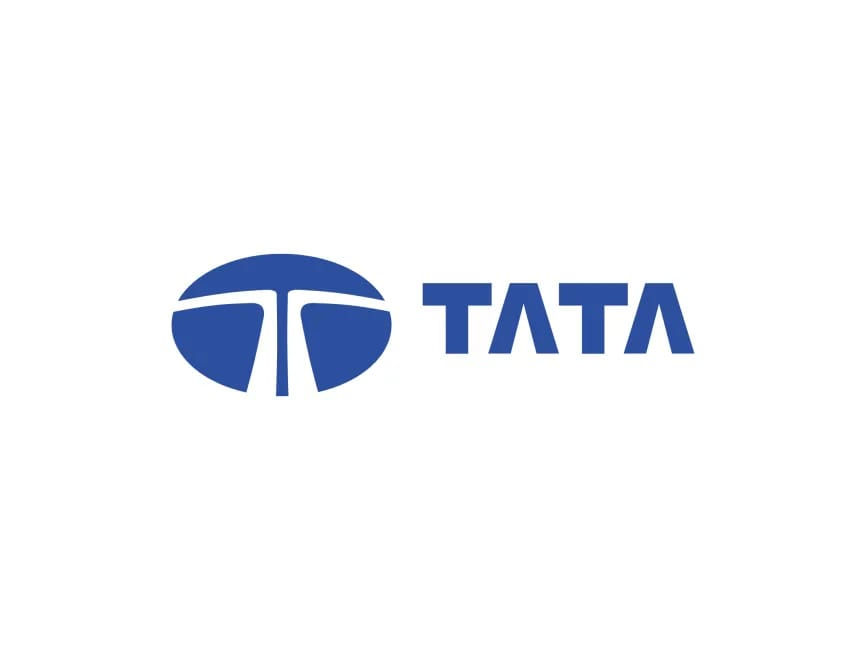
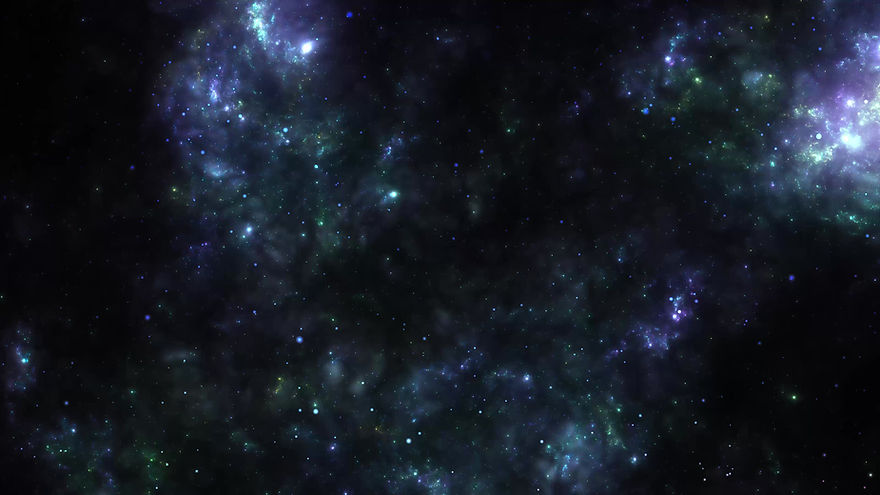
OUR OFFICIAL TRAINING PARTNERS
Through partnerships with top-tier institutions, we provide specialized training that is designed to support students' academic and professional growth.

IIT MADRAS
SAARANG

IIM BANGALORE
UNMAAD
RECOGNITION From
Our Credential Platform Partner
